The pultrusion process is a continuous molding method in which the carbon fiber impregnated with glue is passed through the mold while curing. This method has been used to produce products with complex cross-sectional shapes, so it has been re-understood as a method suitable for mass production and improved production efficiency, and its use is also increasing. However, problems such as peeling, cracking, bubbles, and color difference often occur on the surface of the product during the pultrusion process.
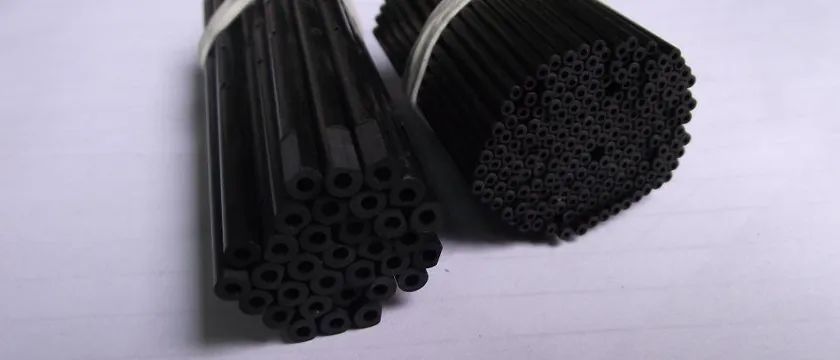
Flaking
When particles of cured resin come out of the mold on the surface of the part, this phenomenon is called flaking or flaking.
Solution:
1. Increase the temperature of the inlet feeding end of the early mold of the cured resin.
2. Reduce the line speed to make the resin cure earlier.
3. Stop line for cleaning (30 to 60 seconds).
4. Increase the concentration of low temperature initiator.
Blister
When blistering occurs on the surface of the part.
Solution:
1. Increase the temperature of the inlet end mold to make the resin cure faster
2. Reduce the line speed, which has the same effect as the above measures
3. Increase the level of reinforcement. Foaming is often caused by voids resulting from low glass fiber content.
Surface cracks
Surface cracks are caused by excessive shrinkage.
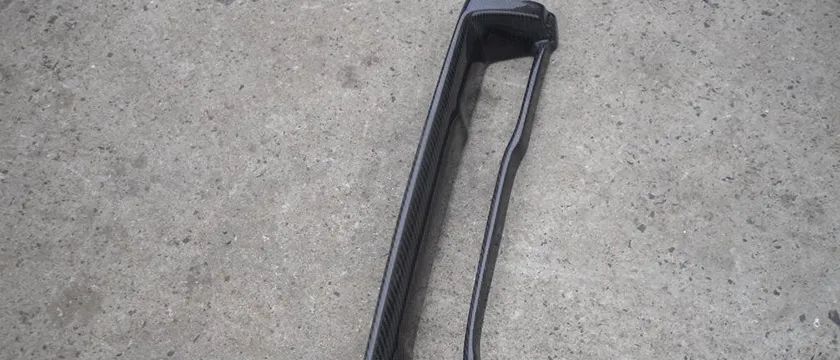
Solution:
1. Increase the mold temperature to speed up the curing speed
2. Reduce the line speed, which has the same effect as the above measures
3. Increase the loading or glass fiber content of the filler to increase the toughness of the resin-rich surface, thereby reducing shrinkage, stress and cracks
4. Add surface pads or veils to parts
5. Increase the content of low temperature initiators or use initiators lower than the current temperature.
Internal crack
Internal cracks are usually associated with an excessively thick section, and cracks may appear in the center of the laminate or at the surface.
Solution:
1. Increase the temperature of the feed end to cure the resin earlier
2. Reduce the mold temperature at the end of the mold and use it as a heat sink to reduce the exothermic peak
3. If the mold temperature cannot be changed, increase the line speed to reduce the temperature of the outer contour of the part and the exothermic peak, thereby reducing any thermal stress.
4. Reduce the level of initiators, especially high temperature initiators. This is the best permanent solution, but needs some experimentation to help.
5. Replace the high temperature initiator with an initiator with low exotherm but better curing effect.
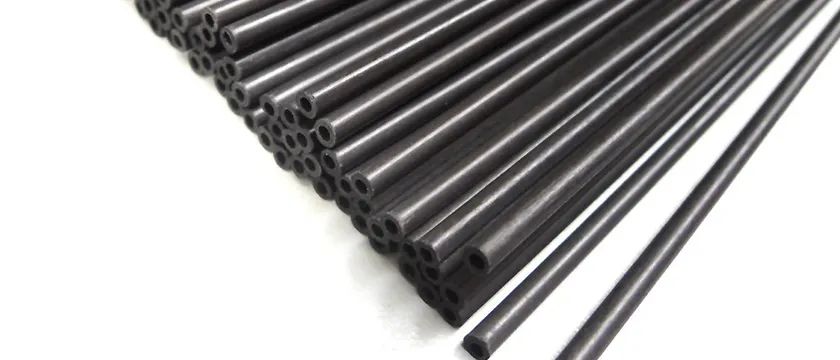
Chromatic aberration
Hot spots can cause uneven shrinkage, resulting in chromatic aberration (aka color transfer)
Solution:
1. Check the heater to make sure it is in place so that there is no uneven temperature on the die
2. Check the resin mix to ensure that fillers and/or pigments do not settle or separate (color difference)
Low bus hardness
Low barcol hardness; due to incomplete curing.
Solution:
1. Reduce the line speed to accelerate the curing of the resin
2. Increase the mold temperature to improve the curing rate and curing degree in the mold
3. Check for mixture formulations that lead to excessive plasticization
4. Check for other contaminants such as water or pigments that can affect the cure rate
Note: Barcol hardness readings should only be used to compare cures with the same resin. They cannot be used to compare cures with different resins, as different resins are produced with their own specific glycols and have different depths of crosslinking.
Air bubbles or pores
Air bubbles or pores may appear on the surface.
Solution:
1. Check to see if excess water vapor and solvent are caused during mixing or due to improper heating. Water and solvents boil and evaporate during the exothermic process, causing bubbles or pores on the surface.
2. Reduce the line speed, and/or increase the mold temperature, to better overcome this problem by increasing the surface resin hardness.
3. Use a surface cover or surface felt. This will strengthen the surface resin and help eliminate air bubbles or pores.
4. Add surface pads or veils to parts.
Post time:
Jun-10-2022